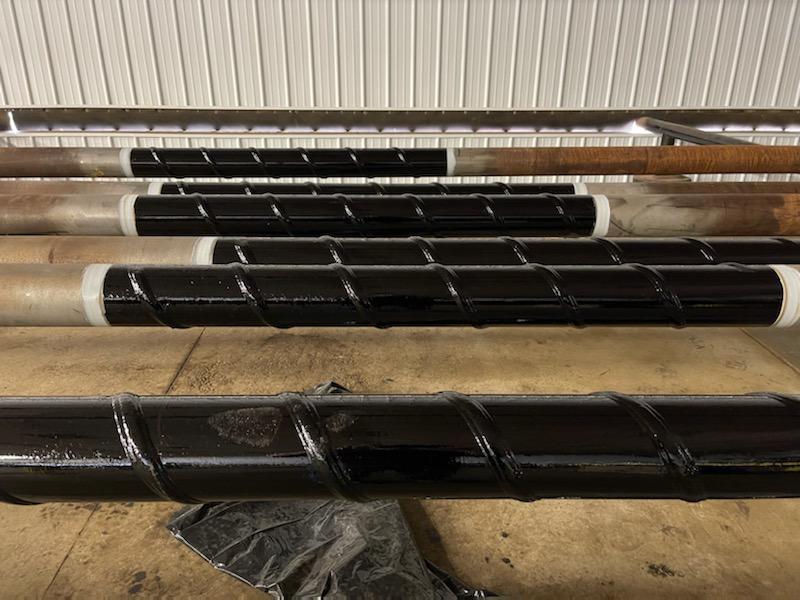
Potential Cost Saving Analysis
Spiralbanding Can Help Save Significant Drilling Costs With Spiralbanding, drill pipe is in the well longer without being rotated top to bottom or replaced, increasing productivity. The cost savings associated with replacing drill pipe less often, and overall increased performance from the drill string are significant. Model of Comparison This analysis uses data from a real-world downhole trial in North Dakota, USA, to explore the potential cost savings associated with the use of Spiralbanding Technology to protect the drill string. Results and actual cost-savings will vary depending on a number of factors in other drilling projects. For this example we have compared Drill Pipe costs for 36 wells drilled, over approximately 18 months, in three differing scenarios. The result of wear on both the Spiralband and Drill Pipe Tubes are extracted from data received from the Drilling Contractor who conducted this trial. Notes/Observations: Drill pipe string without Spiralbanding lasts 12 wells before it’s rejected, including pipe being rotated ‘top to bottom’. Spiralbanding has 50% of its original thickness remaining after 12 wells, is worn down after 24 wells. (Drill pipe without Spiralbanding lasts another 12 wells before it’s rejected) |
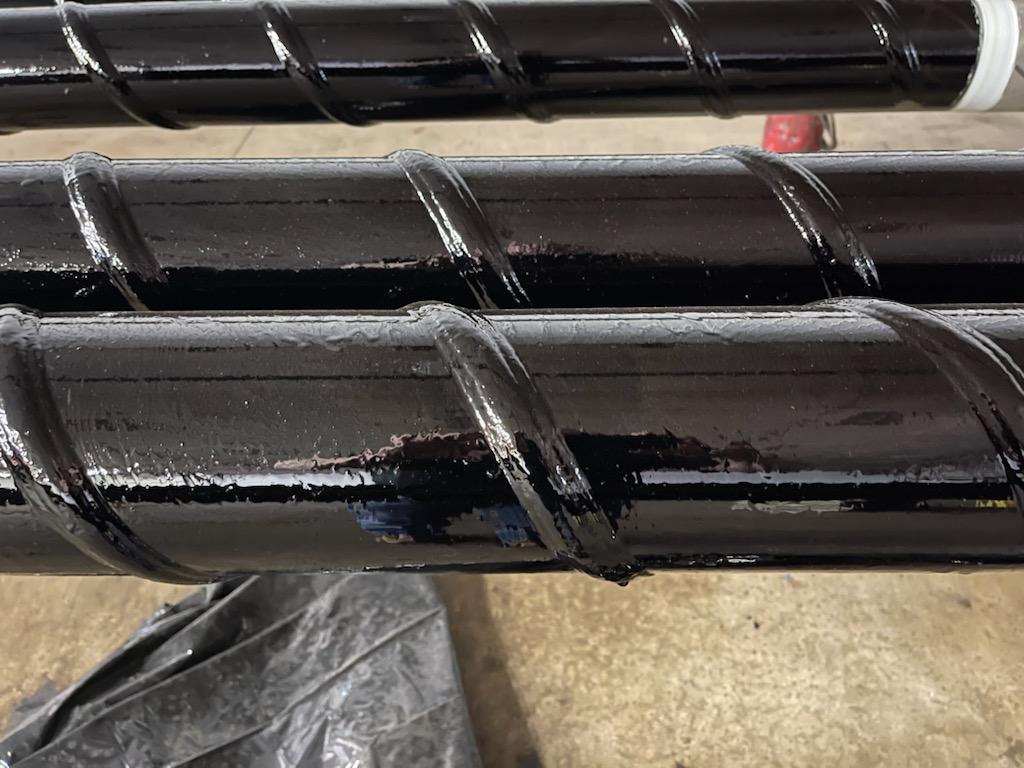
Scenario A – Drill Pipe cost with no Spiralbanding used
New Drill Pipe 22,000ft x 3 - $4,290,000 Total Drill Pipe cost, 36 wells - $4,290,000 Scenario B – Spiralbanding is applied to used Drill PipeNew Drill Pipe 22,000ft (no Spiralbanding) - $1,430,000 Total Drill Pipe cost, 36 wells - $1,613,333 Scenario C –Spiralbanding is applied to new Drill PipeNew Drill Pipe 22,000ft with Spiralbanding
Total Drill Pipe cost, 36 wells - $1,613,333 To download a pdf of this analysis, click here. |